A metering pump or is a positive displacement pump used to pump chemicals or other substances into a process at a very precise flow rate. Usually, injections are given in a tube or chamber into which the liquid flows.
Metering pumps do this in a variety of ways, but in general, it is done by drawing a specific amount of substance into the chamber and then injecting this amount into the desired tube or chamber. In addition to being used in water treatment and food industry, metering pumps have various other applications in chemical, agricultural, medical and various factories.
How metering pumps work
Depending on the model and brand of the metering pump, its mode of operation also varies. But the basis of their work is the injection of a specific amount of substance into the desired site. Metering pumps are usually smaller in size and are powered by small electric motors or pneumatic actuators.
Flow control for these types of pumps is carried out by means of an external control system, or, more commonly, an internal control system that turns the pump on and off. Some of these types have additional features, such as beeping when there is no injectable substance or when the levels of the substance are low.
Metering pump components
The main components of the metering pump are:
- A container for storing injectable substances.
- Foot valve: it is a one-way valve that connects to the suction line and is placed in the tank where the material is injected so that the pump does not exit the suction position. The piece should be heavy enough to stay at the bottom of the tank. In some cases, a hanging indicator is attached to activate the warning horn when the injectable substance runs out.
- Pump: its size and material can vary, but it is usually made of chemical-resistant plastic such as PVC, polyethylene or steel and has two suction and injection heads. The construction of the pump can vary.
- Injection line: it is usually made of PVC material or compressed polyethylene. And in cases of use in steam, boiling water or operation under very high pressures, the material may be steel. The discharge valve, pressure drop and various components of the valve are placed in this injection line.
- Syringe: it is one of the components for injecting the material to the desired place, it is a one-way valve that moves the material through a pump, overcomes the pressure at the injection site, and injects the material into the desired place. A place is required. In addition, this check valve prevents the material from returning to the pump and causing damage after the injection process. The injector has a fountain hole that allows the substance to be injected into the middle of the stream instead of the pipe wall. This causes the injected substance to mix with the target substance.
- Control system: used to ensure accurate measurement of the pump, its operation and shutdown at specified times, it can be as simple as a flow switch or a sophisticated centralized control system with sensors such as PH, chlorine, etc.to increase or decrease the injection dose. Reduces
Different types of metering pumps
There are four different types of metering pumps, which differ in efficiency, pumping mechanism, location and pressure used. The four types are as follows:
Fixed injection diaphragm type
In this type of pump compartment, filling and discharging is carried out via a piston, a diaphragm and valves on the inlet and outlet sides. By pulling the piston, the chamber is filled with an injectable substance and then expelled at a set rate based on a set dose (usually a percentage of the maximum flow).
These pumps are very precise and are usually injected at a constant flow rate of 6 to 250 liters per hour. And with proper control, these pumps can inject different dosages. Examples of grandfoss pumps are DDA and DDE.
Diaphragm pulse jet
The mechanism of action of such pumps is membrane, but the injection is not carried out at a constant and slow rate, the pump is controlled by a solenoid. The coil pulls the substance in the form of pulses and then injects it. The flow rate is controlled by the time interval between pulses. These types of pumps come in mechanical and electrical versions and are generally very simple and inexpensive. Of course, this genre is outdated today.
Metering Cam pump
In this type, a set of feathers pulls a certain amount of sprayed liquid into the pump compartment and sprays it to its destination. Since the size between the feathers is unknown, such pumps are less accurate than membrane pumps.
In addition, the wear in such pumps is also high. They are used when the injection material has high adhesion and is greasy (thereby reducing wear). It is also difficult to install such pumps for low-flow use.
Peristaltic pump metering
These pumps are characterized by a precise and specific injection method. Surgery is performed through a flexible tube through which the injected substance must pass. The pipe is bent in the form of a semicircle and small rollers mounted on a robotic arm move over the pipe. This action pushes the selected part of the injected substance forward and transfers it to the injection part.
This type is used more in the medical field for its ease of sterilization and the possibility of removing and replacing pump parts. A disadvantage of this pump is that it wears out easily and cannot be used for high-pressure injection due to its tube assembly .
Installation of the metering pump
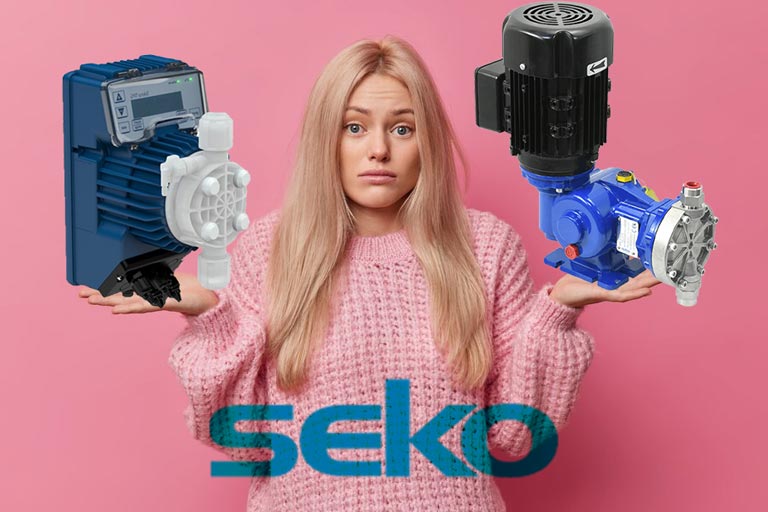
When the metering pump is vented, that is, all the air is removed from the tube and the syringe, the required dose is set or the pump gets its value from an external signal. If the metering pump is working based on an internal signal, it must be calibrated and its dosage adjusted to the required value. When the pump starts to work, it will continue to work until it receives a stop signal.